The idea of a sustainable green recovery from the current global pandemic is one that has been backed by industry bodies worldwide, including IATA, ICAO and ACI. Speaking at the ATAG 2020 Global Sustainable Aviation Forum – Green Recovery event in September 2020, director general of ACI, Luis Felipe de Oliveira, said, “The recovery of the aviation industry will be a key driver of the global economic recovery. To ensure that aviation can continue to provide economic and social benefits, it is crucial that we pursue a green recovery and lay the foundation for a prosperous and sustainable industry for the long term.”
Airports have often led the way in developing buildings that embrace sustainability at their heart, using approaches such as renewable energies, water recycling, natural lighting and innovative ventilation to limit their impact on the environment. But one area that is gaining momentum at the moment is the use of green materials, which are not only sustainably sourced, but also circular in nature.
“Have you ever finished a 1,000-piece puzzle and decided to use the glue included to save your accomplishment? Sure, you’ve turned many hours of struggle into a nice piece of art, but made it impossible to ever do the puzzle again,” says Jonatan Kleimark, senior chemicals and business advisor at ChemSec – the International Chemical Secretariat, an independent non-profit organization that advocates for the substitution of toxic chemicals in products and materials with safer alternatives. “The glue has been absorbed by the cardboard pieces, making them very difficult – if not impossible – to recycle. If your artwork breaks, or you get tired of it, it’s just waste. And if you want to do the puzzle again, you’ll have to buy a new one.”
According to Kleimark, this approach of take, make, waste has been the mindset of the construction and interior design industry for a long time. However, he believes this is now changing and that a shift from a linear to a circular mindset has begun, where the aim is to replace virgin materials with reused and recycled ones to the furthest extent possible.
“Historically, sustainability has come first, not circularity,” he adds. “The road from sustainability to circularity isn’t that far, but steps still need to be taken. A good example is the World Green Building Council’s Health & Wellbeing Framework. Initiatives like these, where sustainability and circularity are part of the mindset from the start, are very important.”
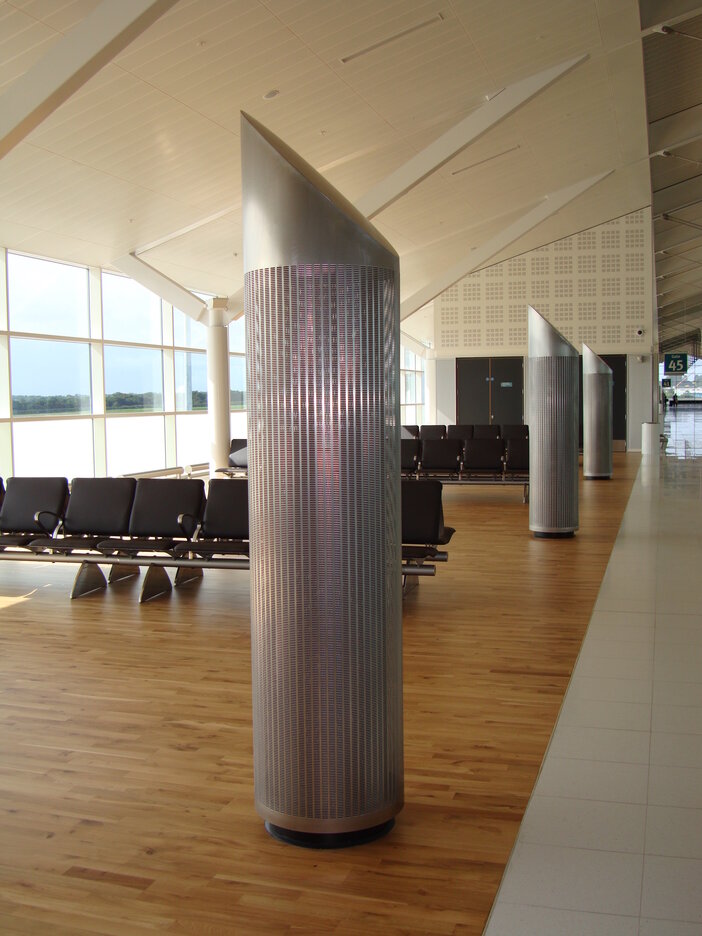
A circular airport
A circular approach is not new to the architectural and development teams of airport facilities. More and more projects are now reusing old materials on new developments, as HNTB’s aviation project director and vice president, Julie Wienberg, explains: “On all our airport projects that include demolition, we specify the recycling of as much demolished material as possible. This includes recycling pavement as sub-base for new airport runways, taxiways and aprons. It also includes recycling metals such as aluminum, steel and copper.”
HNTB also has a big focus on using sustainable materials in all projects, such as locally sourced certified wood and recycled-content aluminum and steel. “Specifically, we look to use engineered wood products that reduce the amount of raw new wood used in the product while improving the performance of the materials,” adds Tom Rossbach, aviation architecture market sector director and vice president at HNTB.
Wienberg continues, “The concrete industry has also made some significant improvements and innovations in the development of concrete that can significantly reduce the CO2 emissions and even sequester CO2 through processes such as CarbonCure.”
According to Rossbach, HNTB was the first aviation architectural firm in the world to achieve a LEED Platinum certification for a commercial airport terminal building for San Diego International Airport’s Terminal Two West project. “The project studied many sustainable options, including geothermal wells and thermal energy storage tanks for the central plant,” he explains. “HNTB performed a return-on-investment analysis for the airport, which focused on a number of sustainable attributes, including 124,000ft2 [11,520m2] of rooftop solar panels, recycled pavement for the new apron and taxiways, a highly insulated building skin, an all-white roof to reflect heat, and graduated tinted glazing for vision glazing to reduce heat gain.”
Meanwhile, Skanska, which is leading the design and construction of the LaGuardia Airport Central project in New York, has also embraced a circular approach to terminal development. “At LaGuardia, we estimated that we would have more than 2,500,000ft2 [232,257m2 ] of gypsum board [plasterboard],” says Scott Cannon, executive
vice president and general manager of Skanska’s building operations in Georgia and South Carolina. “Given the standard installation waste and the local capacity to recycle it, we hoped to be able to divert at least 300 tons. In reality, we more than doubled that and have recycled nearly 700 tons to date. For every 10 tons of recycled gypsum we avoid 2 tons of CO2 emissions – in addition to sending nothing to landfill.”
According to Cannon, Skanska achieved this in a number of ways, including working closely with subcontractors to make specifications clear, and using early project phases to “remove any kinks”.
“We expanded our efforts as we worked on the headhouse and diverted nearly 80 tons of drywall away from landfill and back to the manufacturer,” he continues. “The manufacturer disassembles the drywall scraps; 95% turns back into gypsum powder and the remaining 5% is recycled paper. We had less than 1% of other contaminants. The manufacturer uses the powder to replace up to 25% of the raw materials for new drywall.”
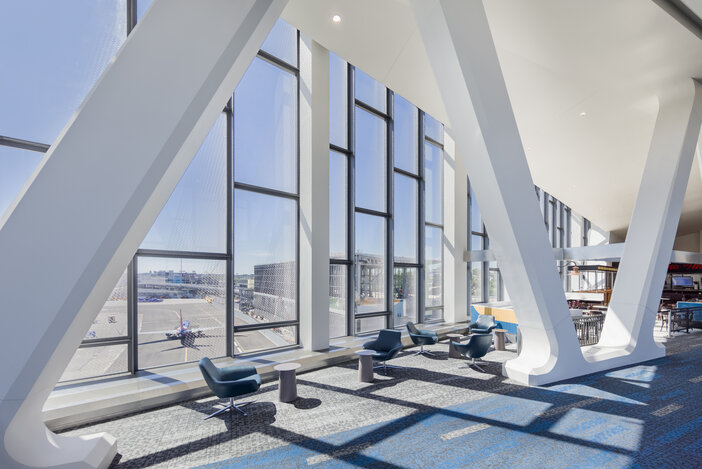
Material transparency
According to ChemSec’s Kleimark, one of the biggest issues faced when trying to achieve circularity in design and development is the transparency of content in materials. “Without that, we cannot know how to treat the goods/material and we can’t ensure that it’s safe for circulation,” he says. “To avoid problematic content – the most important step toward circularity – companies need to understand the content in the material and goods they use, and achieve transparency in the supply chain. From there, the next step is to decide what the problematic content is.”
Kleimark notes that this can be done by compiling lists of restricted substances that specifically ban certain chemicals. “It’s also possible to use existing lists, such as the ChemSec SIN List, which is a science-based list of chemicals with hazardous properties,” he continues. “Certification schemes such as LEED can also be used
for this purpose.”
HNTB’s Rossbach agrees with Kleimark that so-called ‘nutrition labels’ of construction materials are needed to make reuse more achievable. “Most architects and designers are conscientious about the social impacts of their projects and have made huge efforts to push industry sources to share the true content of products,” he comments. “We are also seeing clients often taking a more hands-on, direct interest in what components and materials are being used in their projects as they are now, more than ever, wanting to publicize the health and safety aspects of their projects.”
Wienberg adds, “Buildings are no longer amortized for a 50- or 100-year useful life, as most clients and their lenders want to see a 5- to 10-year ROI with a 10- to 20-year lifecycle. To counter this, we need to design and build projects now, with a view to deconstructing the project in the future, knowing that at most we have a 10-year refinish cycle and 20-year remodel or refurbishment cycle. Understanding how buildings really work and go together as part of a living, breathing system, we can help clients understand the impact of decisions now on the reality of projects in the future.”
As Kleimark says, achieving transparency in the supply chain, as well as for the materials themselves, is important. This is where measuring total embodied carbon comes in – the CO2 emitted during the production of the materials.
“All materials are part of assembly lines,” says Dirk Kestner, principal and director of sustainable design at Walter P Moore. “Therefore we need to look at the Whole Building Lifecycle Assessment (a scientific methodology that can support the efforts of green building professionals to build more sustainable buildings), which enables teams to move beyond an attribute-based definition of sustainability to compare functional equivalent assemblies. This process will illuminate specific assemblies responsible for the greatest portion of the environmental impact.”
According to Kestner, some industries have started to include requirements for design and construction teams to both measure and reduce embodied carbon. “Documents such as environmental product declarations that quantify impacts such as embodied carbon allow teams to make quantified comparisons as part of the design and procurement process,” he says. “Walter P Moore is a pilot sponsor of the Embodied Carbon in Construction Calculator, a tool that enables teams to easily use this data during the procurement process to enhance supply chain accountability.”
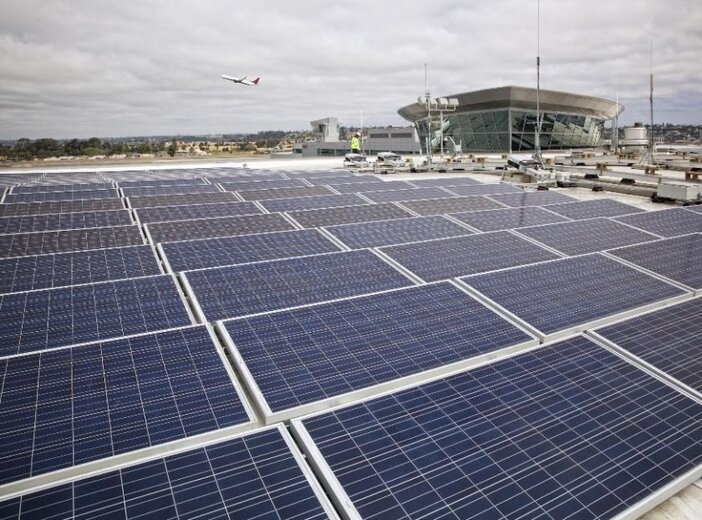
A concrete future
The ultimate aim of a circular economy is to reduce the need for virgin raw material – an important goal given that the world’s natural resources are not inexhaustible. Take sand, for example: “In an article published on worldgbc.org, I refer to a BBC article warning about the depletion of sand suitable for building materials, if the current construction rate and inability to reuse materials continue,” says Kleimark. “It is a harrowing – and mind-boggling – thought that we would run out of a material as commonplace as sand.”
Sand is one of the key ingredients in concrete, which is one of the most widely used materials in the airport sector, and also one of the most environmentally damaging. Walter P Moore’s Kestner comments, “There is an increased industry focus on [the development of] low-carbon concrete. And there is a greater focus on lifecycle assessment and carbon reduction in the design industry, which includes a thoughtful examination of concrete mix designs and making every pound of cement count. Additionally, there have been several technological advances with new cement alternatives, cleaner processes, and the advancement of carbon capture and sequestration.”
Edgar Bohner, research team leader and project manager (structural materials) at the VTT Technical Research Centre of Finland, adds, “Concrete is by nature a composite material, made up of cement binder, aggregates (sand, gravel and rocks) and water, containing a wide selection of local materials, thus allowing for multiple ways to improve sustainability. There are three major strategies to do this: substituting cement, which is responsible for the majority of CO2 emissions, with abundant natural or industrial mineral materials; using concrete to recapture CO2, thus contributing to offsetting the emissions released when manufacturing the materials; and full circularity of all components of concrete via beneficial reuse.”
According researchers from VTT, the right building materials for circularity already exist today, but there are still challenges that need to be overcome. “Achieving both technical and economic feasibility for the beneficial reuse of existing building materials is the main focus in pursuit of a full circular economy. There is also room and need to develop more sustainable chemicals, which could also be bio-based,” adds Bohner.
“Fit for circularity also means that the buildings must be designed differently, so that they can be flexible and that it is possible to take the materials and use them somewhere else. Many of the products that are closer to fulfilling circularity, such as steel, benefit from being relatively homogeneous in comparison with concrete. While the heterogeneity of concrete represents a major technical challenge, the flexibility of concrete to incorporate a diverse spread of mineral materials can synergize with the need of other industries in pursuing circularity with their end-of-life products,” he concludes.
This article was originally published in the April 2021 issue of Passenger Terminal World.