With this in mind, San Francisco International Airport (SFO) opted to design and build its new Harvey Milk Terminal 1 in a way that would reduce its environmental impact. Embodied carbon analysis was used throughout the design and construction process to help project managers make informed decisions about the building materials used. This led to the team smashing its goal of achieving a 10% reduction in embodied carbon footprint from the baseline.
Harvey Milk Terminal 1 reconstruction
The reconstruction of SFO’s Harvey Milk Terminal 1 had been discussed for almost 20 years before work began, but those involved, such as program manager Kristin Allen, are glad they waited as this enabled them to incorporate many more modern, sustainable features that might not have been considered a decade or more ago.
The work consisted of a full rebuild of the terminal – an area covering 111,500m2 – to renovate the building, improve sustainability and increase capacity from 10 million passengers per year to 17 million.
“It wasn’t just about decarbonized building materials, energy efficiency or air quality”
Anthony Bernheim, SFO
“We have a new check-in lobby, screening checkpoints, baggage system, 27 gates and a new aircraft parking apron,” Allen says. “It’s a very large facility serving multiple domestic airlines, plus we have seven international swing gates that we can handle international arrivals on.”
The project, valued at US$2.5bn, was completed in phases, the first concluding in 2019, followed by subsequent openings in 2020 and 2021 before the final phase reached completion in June 2024.
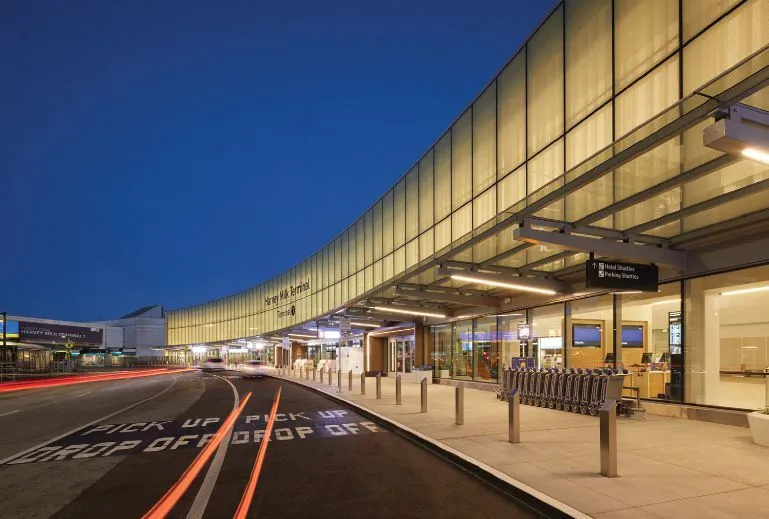
Whereas many teams may have to work hard to get buy-in from the boardroom for a project focused on reducing embodied carbon, in the case of SFO the board was leading the charge.
“This is because sustainability is one of SFO’s strategic goals,” says Allen. “The board members are the ones giving us the freedom, bandwidth and encouragement to go out and do these things.”
Over the years the airport has worked hard to become more sustainable and runs very efficiently. For example, all the airport’s electricity is carbon free, generated through the Hetch Hetchy Regional Water System. However, SFO had noted that most of its carbon emissions were coming from construction materials and activities, a finding underlined by a UN report showing that embodied carbon emissions from the building sector produce 11% of annual global GHG emissions.
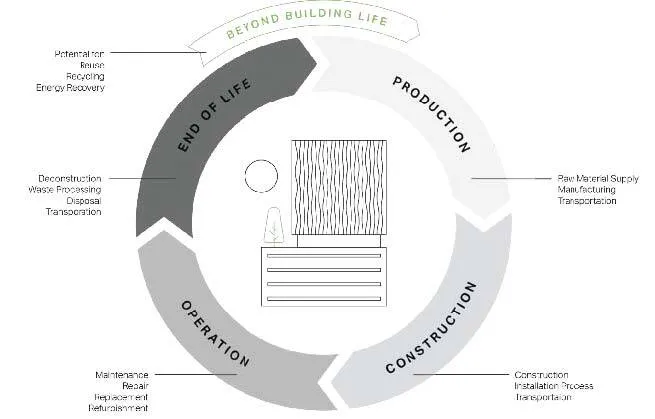
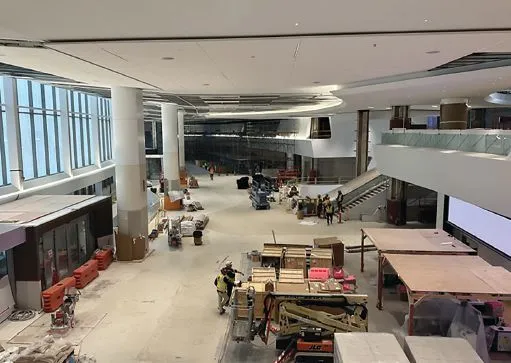
The search for synergy
Finding the right partners was key for SFO, and the organization used a simple request-for-proposal approach to do so.
“We don’t have bridging documents; we have project requirements and do a best-value procurement based on a technical proposal and an oral interview. It’s about bringing your best team – the key personnel – to come and answer questions live from our panel. There’s no business development people or presentations allowed,” Allen notes.
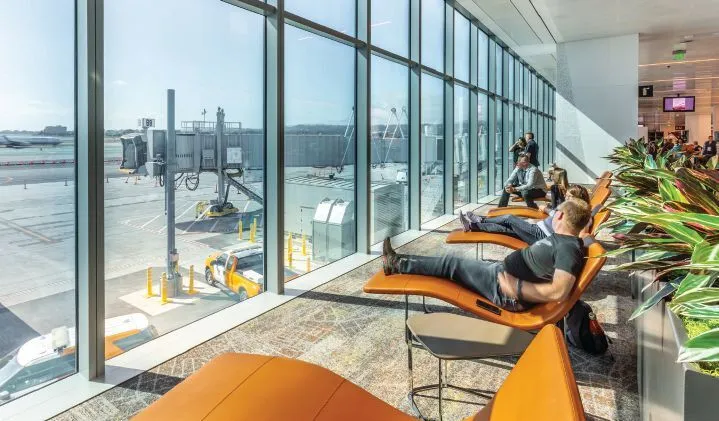
The 80-20 rule
In terms of reducing its embodied carbon in this project, SFO focused on the 80-20 rule, also known as the Pareto Principle.
“What are those 20% of materials causing 80% of the impact?” says Kirsten Ritchie, principal and global director of climate action and sustainability at Gensler. “Initially this meant focusing on the foundations and structure – so steel and concrete.

In terms of concrete, SFO was fortunate in that the Bay Area’s ready-mix suppliers were already quite progressive in terms of coming up with lower-carbon materials. “They actually helped pioneer the Environmental Product Declaration (EPD) process for every batch of concrete,” says Ritchie.
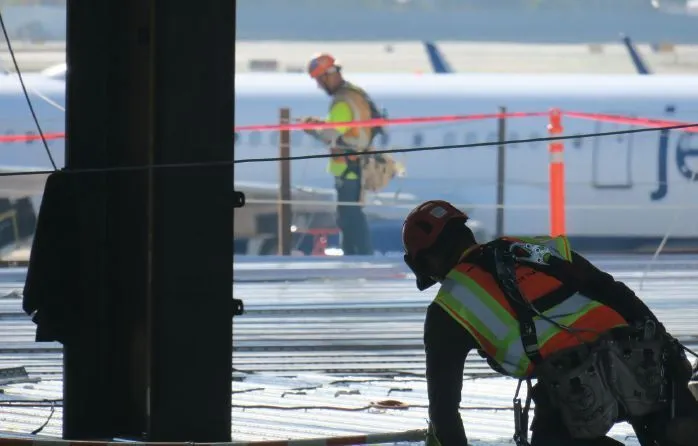
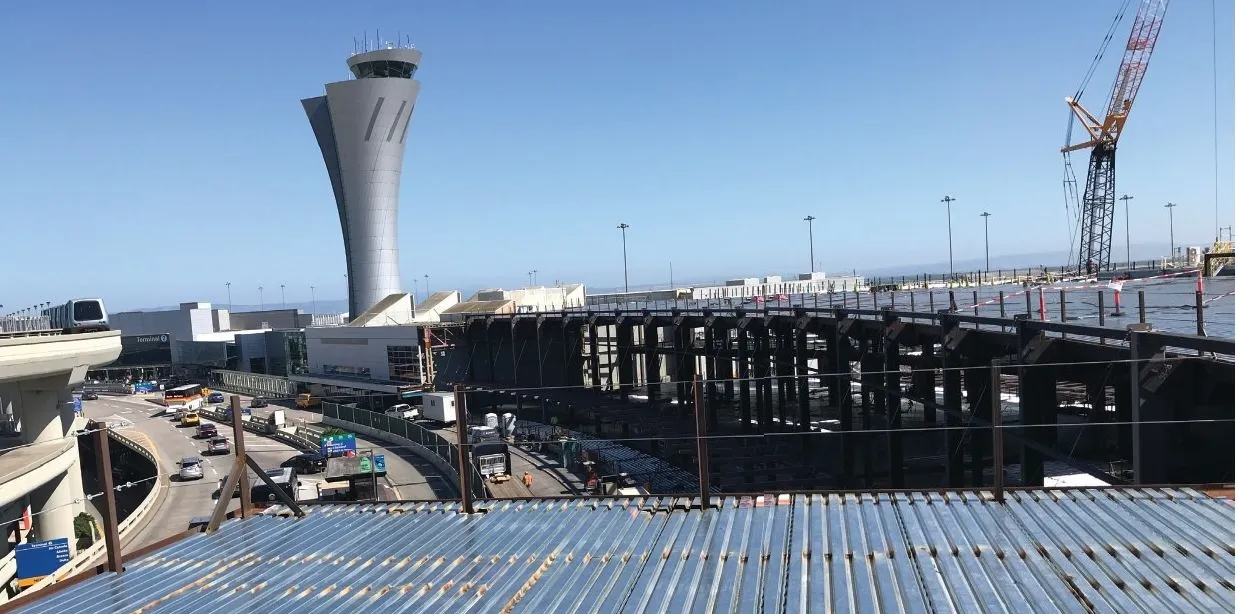
The carbon footprints of materials for flooring, roofs and walls were also studied closely to ensure the team used the best materials to reduce the embodied carbon impact.
“What are those 20% of materials causing 80% of the impact?”
Kirsten Ritchie, Gensler
“We were drilling down on all those different material types and continue to work with those industries to help drive lower-carbon products,” says Ritchie. “There were some products and systems that we were able to get EPDs for, and some companies used those to really improve their product – the baggage handling system, for example. So, there were some successes in driving the industry in this direction.”
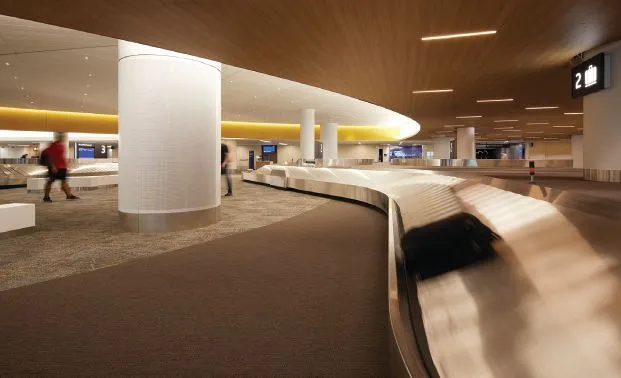
Final works on Harvey Milk Terminal 1 were completed just a few months ago and all those involved are overjoyed with the final results in terms of embodied carbon reductions.
“Having never done anything like this before, the team set a realistic reduction target of 10%. The final outcome was over 20%, which is pretty exciting,” says Ritchie.
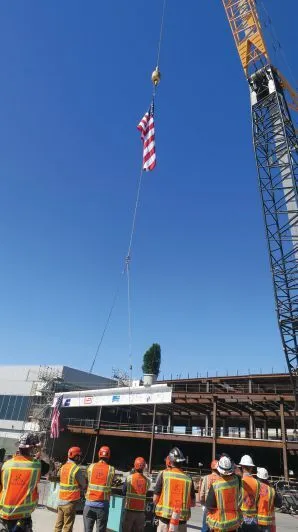
The team is wrapping up the project by finalizing SFO’s updated sustainable planning, design and construction standards. These should be available online by the time this magazine goes to press.
“Lessons learned have helped us formalize our guidelines into standards, which will be built into future design-build contracts,” Bernheim says.
“Standards are requirements, but we have also introduced two additional ‘stretch goals’, so it’s ‘good, better and best’,” he continues. “These are living documents, so we can update them on a regular basis as the industry progresses. We can only do so much at this time, but we know the industry is moving forward.”
Allen adds that the impact of the Harvey Milk Terminal 1 project goes beyond the airport itself, and has caused a ripple effect across the design and construction industry. “We watch, listen and learn from each other, and by sharing our experiences we’re seeing more people get on board the train. They’re realizing there are better ways to do things.”
Bernheim continues, “It’s been interesting in that with the projects we’re now starting up, potential partners are coming in ready to talk about sustainability and resilience right off the bat. They’re coming in prepared and want to be involved in this movement, something that may not have been the case in the past.”
Top tips to reduce embodied carbon
SET CLEAR GOALS
“It’s important that at the onset of a project, clear goals and targets are defined in coordination with the client and communicated to the design team,” says Varun Kohli, principal and director of sustainability at architecture and design firm Corgan.
Lifecycle analysis/assessment (LCA) boundaries, processes and goals – whether driven by the airport’s own aspirations or in alignment with Leadership in Energy and Environmental Design (LEED) or other third-party certifications – should be defined early in the project.
“Without a team effort, LCA reductions are not possible in complex projects such as aviation facilities,” continues Kohli. “This means that the structural engineering team is looking at options for structural materials and that the architectural team is looking at envelope assemblies to assess all materials.”
DON’T FORGET THE FOUNDATIONS
“It’s important that system and material optimizations include foundations when considering carbon reduction, as airport foundations can be the main contributor to a project’s embodied carbon,” explains Claire Moore, director of engineering at design, architecture, engineering and planning company HOK.
“Sometimes, longer spans can lower embodied carbon by omitting foundation elements. Performance-based specifications have been key to successfully lowering embodied carbon in these foundation elements,” she continues.
“At the new Salt Lake City International Airport passenger terminal, for example, we incorporated significant amounts of fly ash into the foundation as a cement replacement. This lowered the embodied carbon of the overall foundation system for the new hub airport.”
TAKE A HOLISTIC APPROACH
“I recommend looking at carbon emission reductions in a holistic way,” says Corgan’s Kohli. “Consider whole building lifecycle assessment (WBLCA) that includes embodied carbon in materials (cradle to cradle), construction-activity-related emissions and, of course, operational energy and carbon for the facility.
“Using a cradle-to-cradle assessment of the materials used forces us to think about circular economy and how materials from the project may be reused at the building’s end of life. Such a systems approach will ensure an efficient process that delivers a successful project.”
BE FLEXIBLE
“These are large projects that can take years, so a lot can change, whether that’s technology or materials. You can really benefit from allowing some adaptability and flexibility – this is part of our progressive design-build process,” notes Kristin Allen at SFO.
“If you’re not willing to make changes along the way, by the time you open you’re going to be behind the curve.”
DON’T BUILD WHEN YOU CAN RENOVATE
“Consider remodeling or significant renovations to avoid embodied carbon emissions associated with new construction,” says HOK’s Moore.
USE EFFICIENT DESIGN STRATEGIES TO REDUCE MATERIAL USE
“Using computational design tools can help optimize building structure, thereby reducing material (be it concrete or steel),” concludes Corgan’s Kohli. “This helps reduce not only embodied carbon but also capital cost for the project.
“We’re starting to see many digital design tools such as ones to help reduce steel connection material, again reducing material, embodied carbon and cost.”
ENSURE ACCOUNTABILITY
“From a consultant and designer perspective, it’s really important to hold each team accountable for their performance,” says Gensler’s Kirsten Ritchie.
“As a minimum they want to be quantifying the carbon footprint, measuring it and providing that information on a periodic basis. Where you can start being progressive is holding them accountable for specific carbon reduction goals.
“If that’s made clear early on, they understand the importance you’re putting on this and it is a definite way to drive measurable improvements.”
This article originally appeared in the September 2024 issue of Passenger Terminal World. To view the magazine in full, click here.