Seattle-Tacoma International (SEA) is one of the busiest airports in the USA, handling 51.8 million passengers in 2019. Its international passenger numbers have doubled over the past 10 years to 5.7 million in 2019, meaning that the original 1970s international arrivals facility (IAF) is no longer fit for purpose.
In 2014 the Port of Seattle, which operates the airport, decided to begin work on a new, much larger IAF to keep up with demand. “Our original completion date for the project was June 2020, but with Covid-19 we are a little late. We now plan to be completed by summer 2021,” says Janet Sheerer, capital construction project manager at the Port of Seattle.
Aside from the sheer scale of the new building – 41,806m2, with an iconic aerial walkway that will span 238m across and 26m above an existing taxi-lane and connect the South Satellite to the IAF – this project is notable for the way in which it is being delivered.
“We’re using a progressive design build [PDB] model, which means we hire a designer and a contractor as a team [SOM and Clark Construction] and they have a lot of the responsibility for managing the design and coordinating among themselves as the design progresses,” Sheerer explains. “It means they utilize fast-track construction, so they put out the design packages in the order in which they need to start building them, and they start building the work as they’re finishing off designing the later packages. It compresses the schedule and creates a much more collaborative process.”
The PDB model had only been approved in the state of Washington a few months before SEA decided to use it. IAF is one of the first projects in the USA to use the method. “It was a pretty bold move by the Port of Seattle to decide to use this new design method, especially on this really critical facility. It is complex because you are always designing and trying to keep up with the budgeting process, but it is supposed to be a ‘no surprises’ methodology, by which I mean at least if you’re going over budget, you understand why along the way,” Sheerer continues.
The maximum budget for the project was set at US$968m, but with Covid-related delays the team had to go to the Port Commission on January 11, 2021 to ask for an additional US$18m to cover staff costs, bringing the full program total to US$986m.
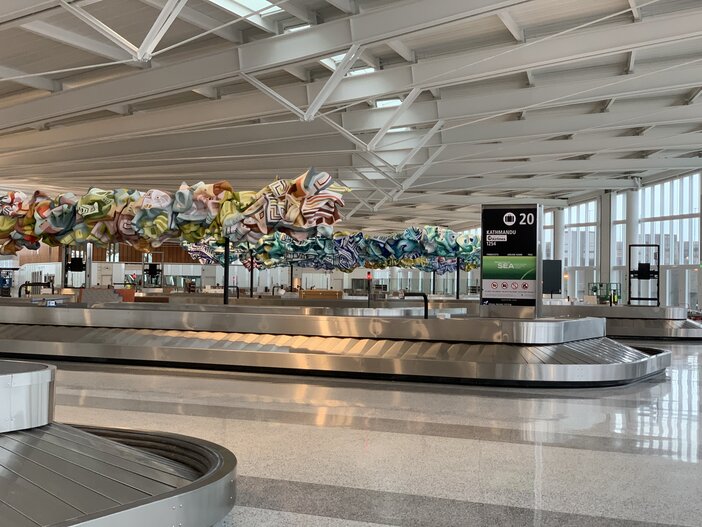
Sense of place
Taking inspiration from the nature that surrounds it, architects SOM designed the new facility to create an immediate sense of place for all arriving passengers. “One of the unique design opportunities for the IAF was creating a visual connection to the stunning landscape, allowing arriving passengers to immediately experience the changing sky and forest of trees, with views of Mount Rainier and the Olympic range,” explains Michael Duncan, design partner at SOM. “The team was inspired to create a procession of light-filled spaces that celebrate this connection to the landscape while seamlessly moving passengers through the international arrivals process.
“The IAF’s architecture has a lightness that complements the existing adjacent terminal, with strength and elegance inspired by the cranes throughout the Port of Seattle,” he continues. “This powerful structural expression can be seen throughout the IAF, but most notably on the pedestrian aerial walkway that spans the airplane taxi-lane. The cables, beams and fittings are pulled inside the walkway and provide crossing passengers with a close-up experience of the bridge’s structural elements.”
That walkway, which is the largest walkway over an active taxi-lane in the world, will take passengers from the South Satellite into the IAF, which is adjacent to the existing Concourse A. As soon as passengers come off the bridge, they will enter the IAF through a wood portal that frames the view of the airport and welcomes them in, according to Sheerer. “It creates a moment. You immediately walk into an open mezzanine space and the idea was to create a sense of arrival. There are local woods and big views, which is one big change. Our existing facility is underneath the existing South Satellite, so the new IAF is a light-filled building and shows a connection to nature, which is really important to us in the Pacific Northwest.”
It was important to Sheerer that the design of the new facility be really intuitive. From the mezzanine area, passengers can immediately see the baggage carousel and beyond that the Customs and Border Protection (CBP) podiums. “The big difference between this and the old facility is you get your luggage before you talk to a CBP officer for inspection. Following inspection using facial recognition technology, you’ll head down a sloped walkway into the existing Gina Marie Lindsey Arrivals Hall,” she says.
There is a courtyard space between the existing Concourse A and the IAF, which has been turned into a mini forest to provide an immersive experience for arriving passengers. “Douglas Fir is used throughout the interiors and an evergreen forest is planted in the courtyard between the two terminals, which passengers descend into, starting at the top of the trees to the ferns on the ground. At the end, travelers cross a creek between large granite slabs into the meeter/greeter area. It is an evocative journey that creates a dramatic sense of place,” SOM’s Duncan explains.
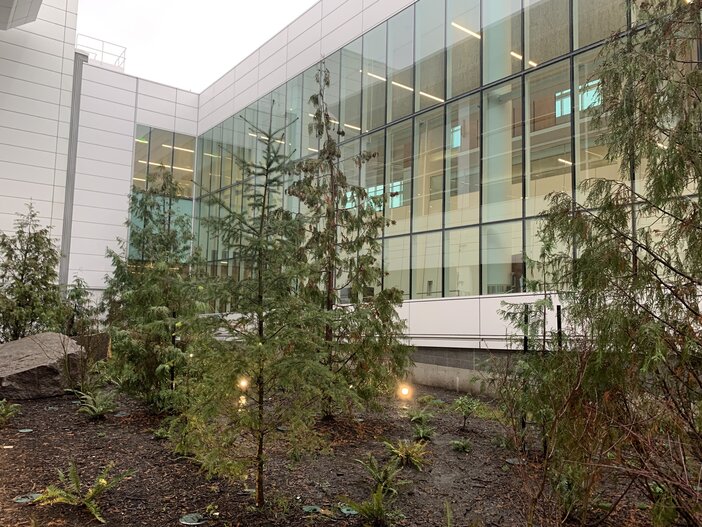
Increased operations
On the face of it, the IAF is not filled with new technology, because the design team preferred to keep it simple and intuitive for passengers. However, the facility features enhanced technologies at border control for faster passport clearance, a new baggage handling system and an increase in baggage claim carousels from four to seven.
Sheerer adds, “We have programmable displays that can be modified – each baggage claim has four 98in monitors that will display all the necessary information, but we made sure the ability to change that on the fly was built in. There is also biometric technology at border control, and security and surveillance technology within the building that passengers won’t see or even notice. It’s just there to keep the passenger safe. We want them to go through the facility as efficiently as possible without a focus on technology.”
The use of new swing gates in Concourse A also means the airport has nearly doubled its international gate capacity from 12 to 20, and passenger capacity has more than doubled to 2,600 passengers per hour. “We’ve added the swing gates into Concourse A through building what we call pods,” explains Stephen St Louis, lead construction manager/project manager at the Port of Seattle. “Between these pods is a series of doors that get controlled. So, if it’s an international flight, certain doors are closed and others open, and vice versa for domestic flights. That’s one of the ways we’ve been able to grow the international capabilities here at SEA.”
There are no concessions in the IAF because regulations don’t allow them, but there are plenty of new restrooms, a nursing room, pet relief, a VIP lounge and customer service desks. There are 12 Global Entry kiosks and a baggage recheck area for passengers who need to recheck their bags for another flight. There are also automated kiosks for those same connecting passengers. “The exit after the security checkpoint for transfer passengers ends up on Concourse A right in front of the brand-new marketplace, so even though we weren’t able to put any of those concessions inside our facility, it is right in front of you as soon as you’ve been processed,” Sheerer adds.

Complex bridge operation
One of the most challenging parts of the IAF project has been the construction of the connecting walkway. First, the sheer size of the walkway meant that specialist steel fabrication firms needed to be sourced to create the frame, which was too large to construct on-site.
Stephen St Louis explains, “At one point we had seven shops fabricating different components of the bridge. Once we overcame the steel fabrication issues, we then had to erect the bridge. We constructed the 320ft [98m] center section at Cargo 2, a site about two miles [3km] away at the north end of the airport, and then transported it to the IAF site for erection.”
The transportation and erection of the massive center section took months of meticulous planning by St Louis and his team, as well as several structural engineers and experts on bridge failures and heavy-lifting contractor Mammoet. “Part of the pre-planning required the contractor to do a complete topographic survey of the entire bridge move route so the structural engineers could analyze in a model all of the stresses that the bridge would be undergoing as it was transported,” St Louis says. “There were more than 120 strain gauges placed throughout the bridge steel that were monitored throughout the entire move. They had ranges – green, yellow and red; as long as the numbers stayed within range, we could keep on moving. Fortunately, everything went smoothly.”
There was a seven-day taxi-lane closure for the bridge move and the entire process took 11 days in total in February 2020.
This article was originally published in the April 2021 issue of Passenger Terminal World.